WE ARE ENELEX
Vyrábíme a celosvětově dodáváme komplexní systémy řízení kvality uhlí, biopaliv a ropných břidlic.
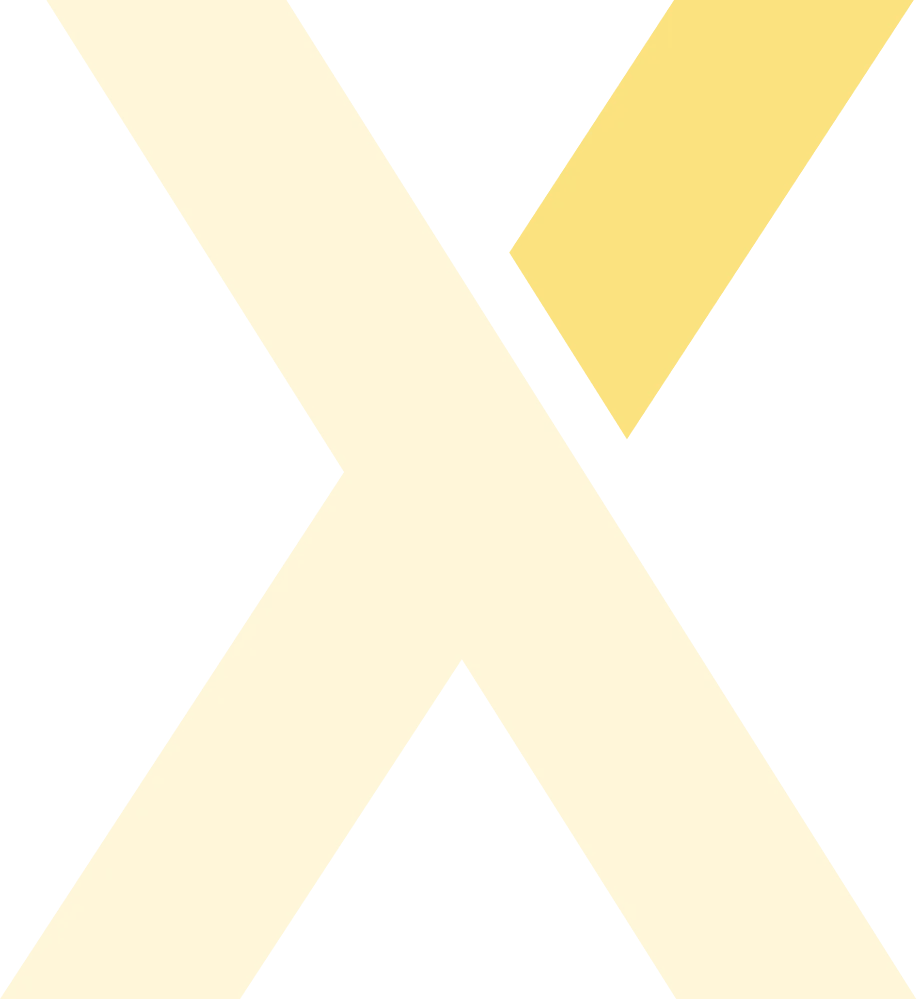
Přední světový výrobce
v návrhu a realizaci systémů řízení kvality uhlí
Patříme mezi přední světové výrobce speciálních elektronických přístrojů a mechanických vzorkovačů paliva pro hornictví a energetiku. Specializujeme se na návrh a realizace systémů řízení kvality uhlí „Coal Quality Management Systems“ pro homogenizaci uhlí a speciální termovizní systémy protipožární ochrany.
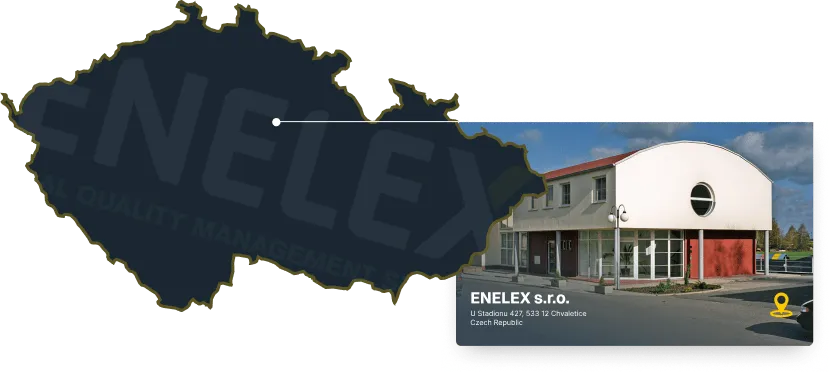
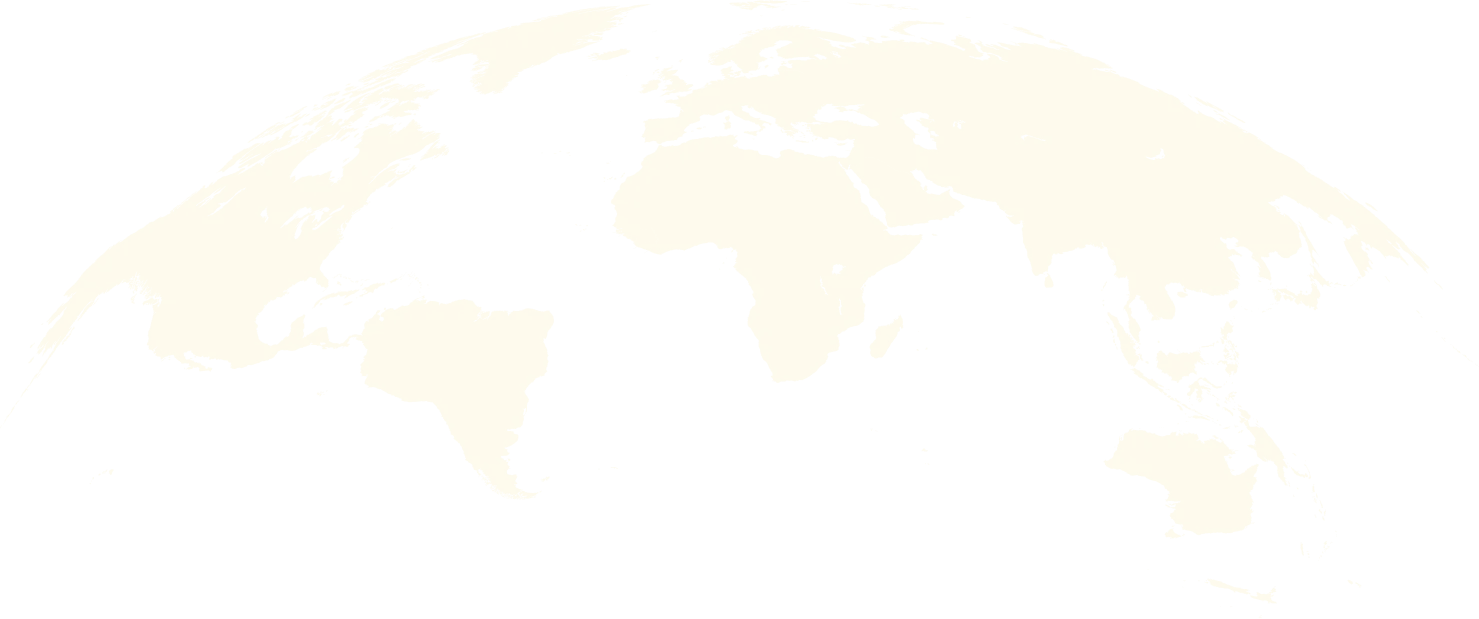
.webp)
Systém řízení kvality uhlí
využití on-line analýzy
Systémy řízení kvality je možné aplikovat v různých fázích zpracování uhlí. Lze je využívat v celém procesu zpracování uhlí od řízení těžby až po bilanční kontroly zauhlování elektrárny.
těžbu uhlí
spalování uhlí
zpracování uhlí
Produkty pro řízení kvality uhlí
Komplexní systémy pro řešení kvality uhlí na klíč, analýzu kvality uhlí v reálném čase (on-line), dále automatické systémy vzorkování veškerých sypkých hmot z pásových dopravníků, kamionů, železničních vagonů, zabezpečovací a protipožární termovizní systémy.
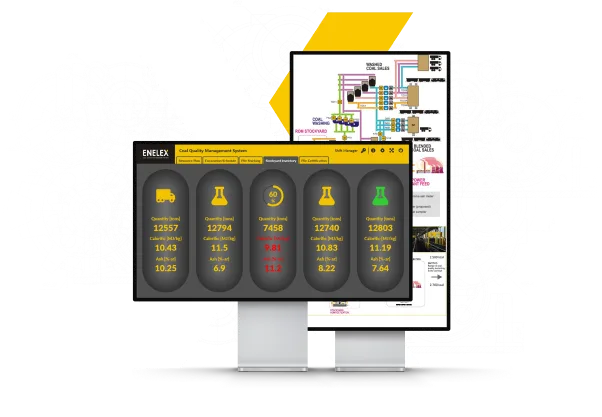
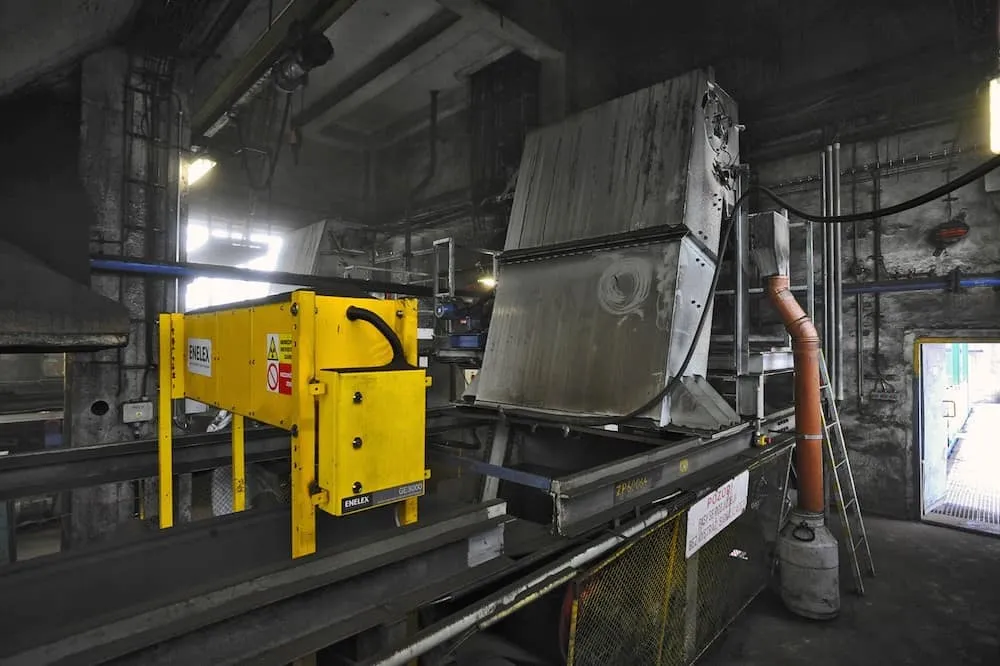
On-line radiometrické analyzátory kvality uhlí
On-line radiometrické analyzátory kvality uhlí
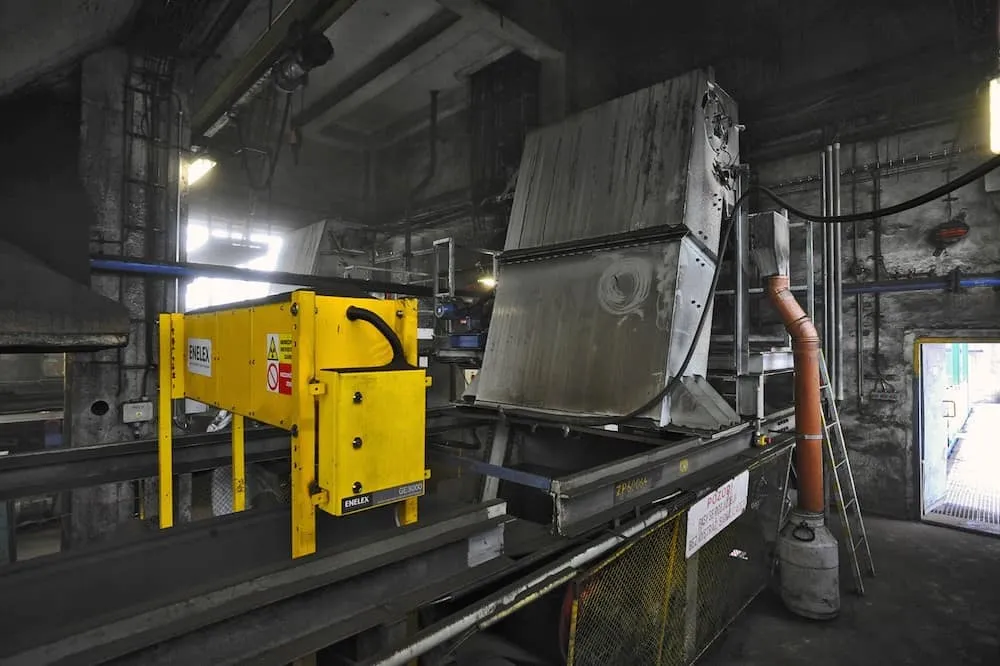
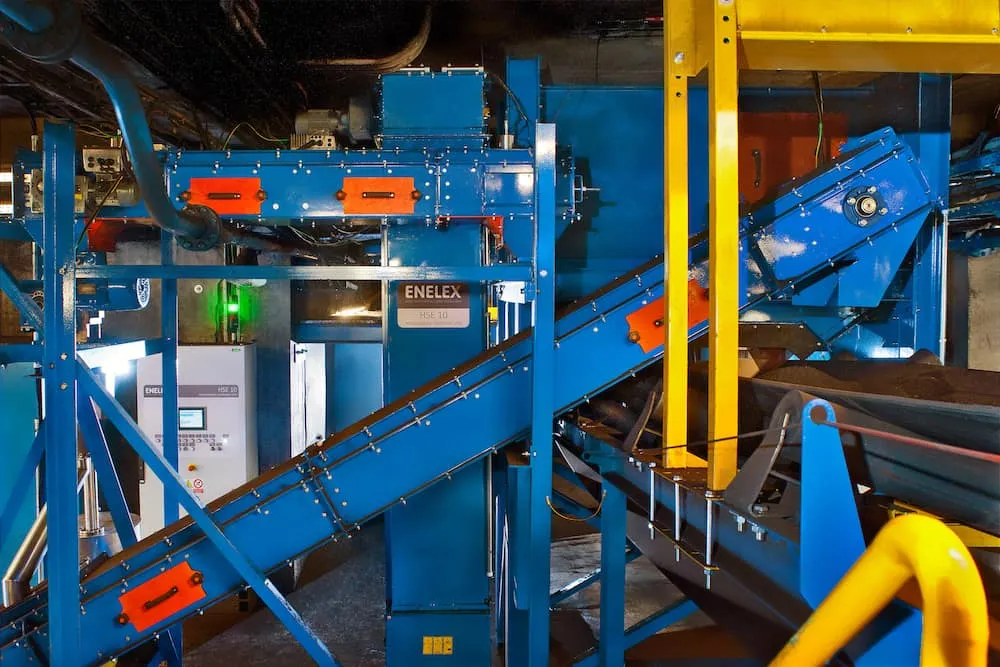
Automatické vzorkování z pásových dopravníků
Automatické vzorkování z pasových dopravníků
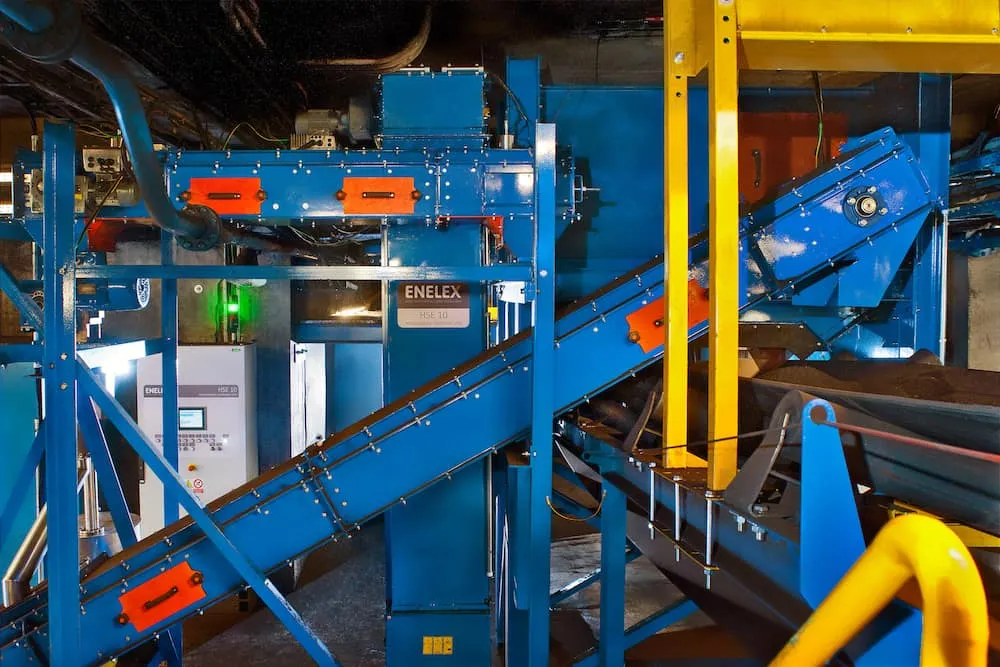
.webp)
Automatické vzorkování z kamionů a železničních vagonů
Automatické vzorkování z kamionů a železničních vagonů
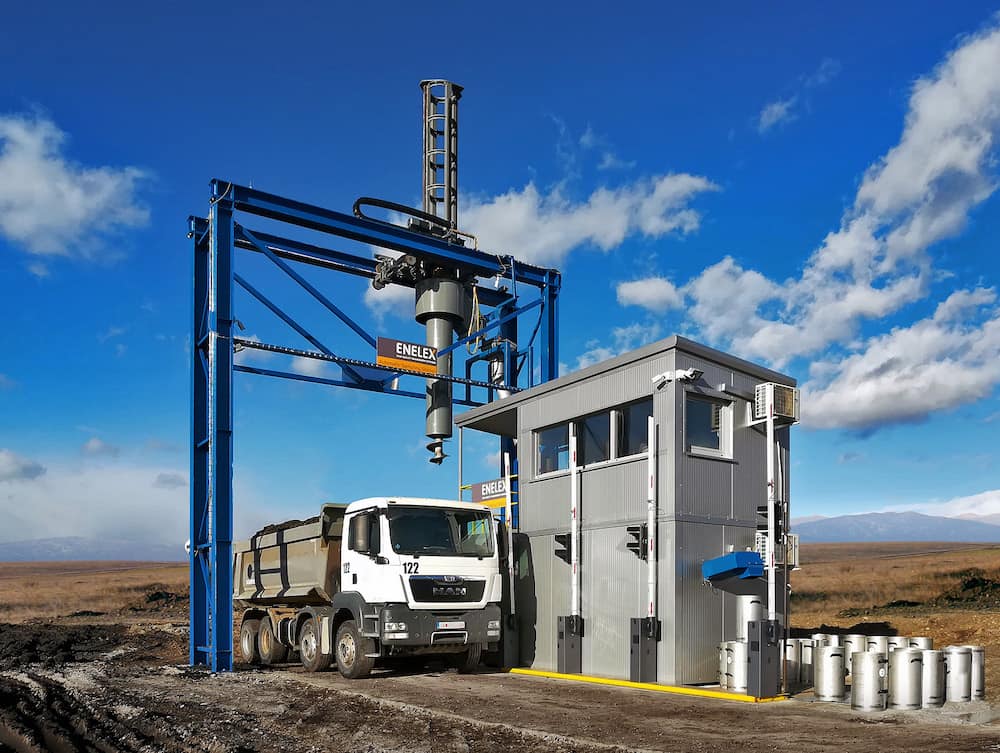
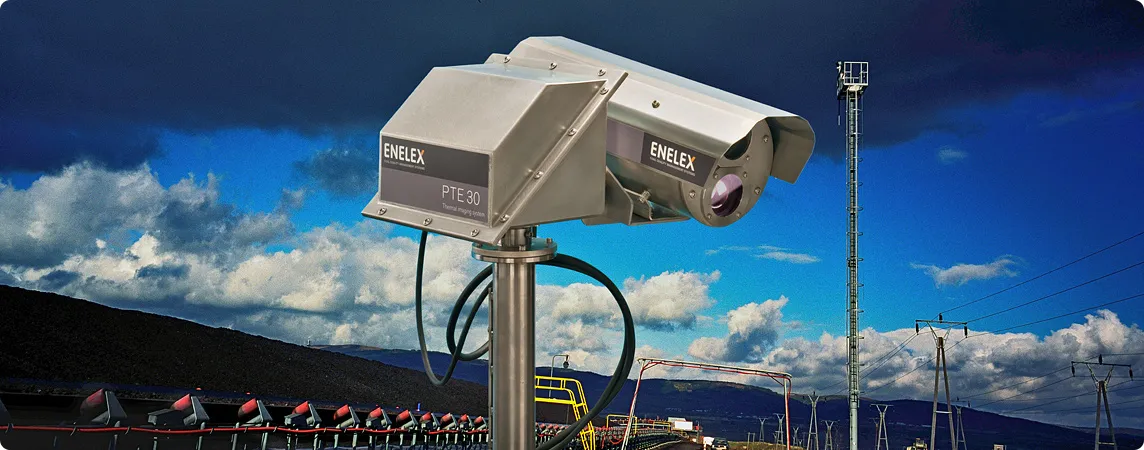
Průmyslové termovizní systémy protipožární ochrany
Průmyslové termovizní systémy protipožární ochrany
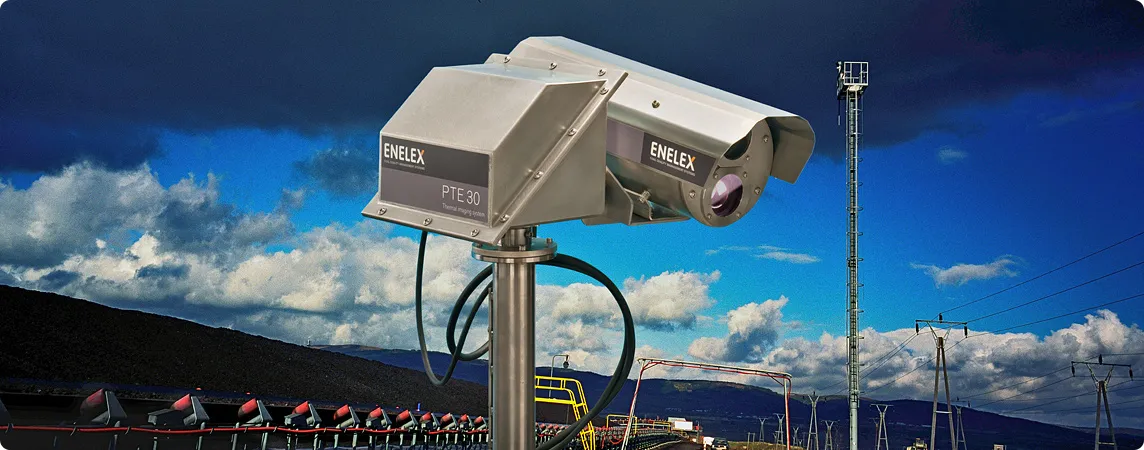
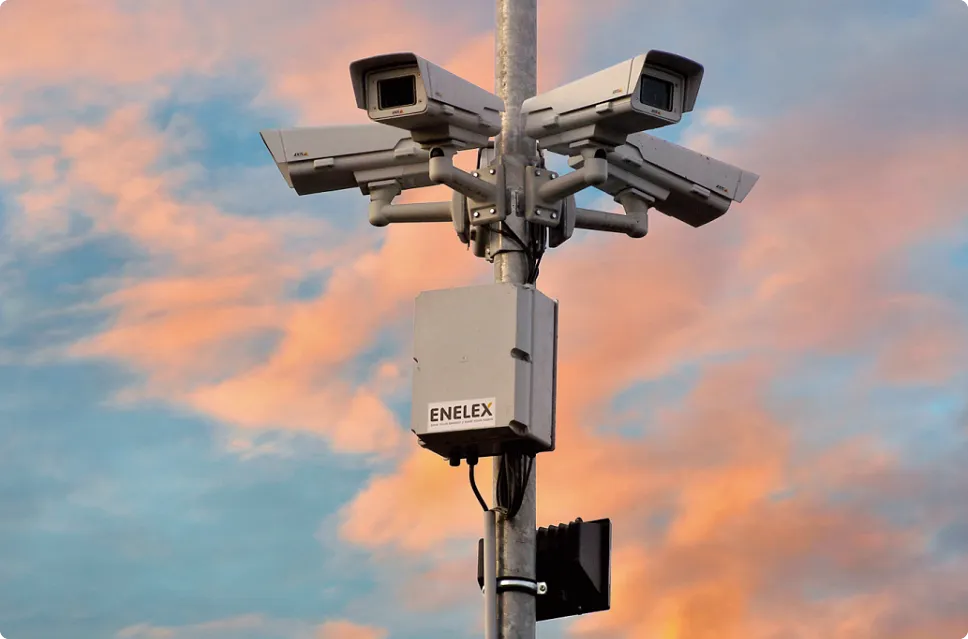
Kamerové systémy
pro těžký průmysl
Kamerové systémy pro těžký průmysl
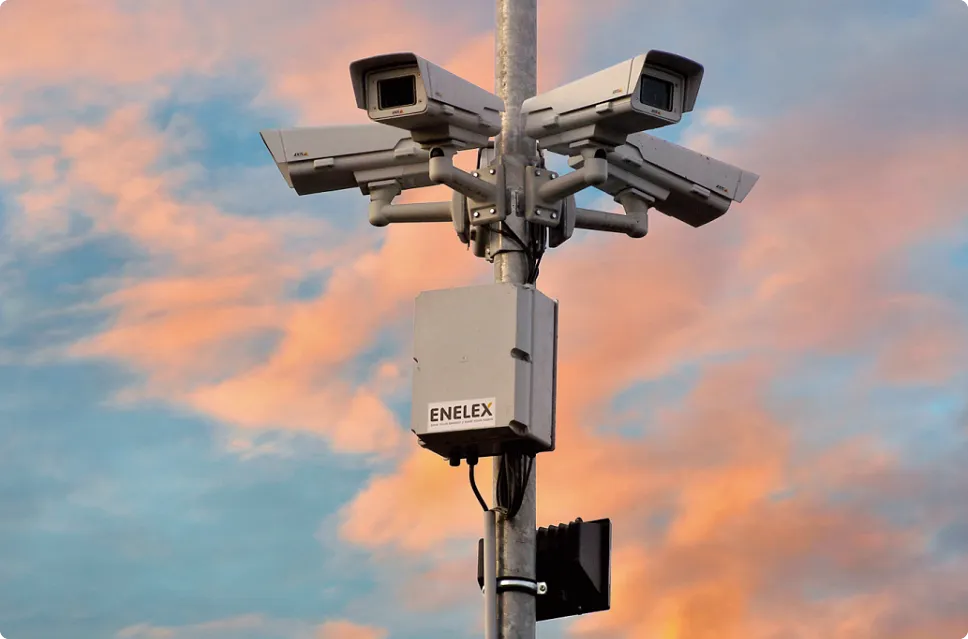
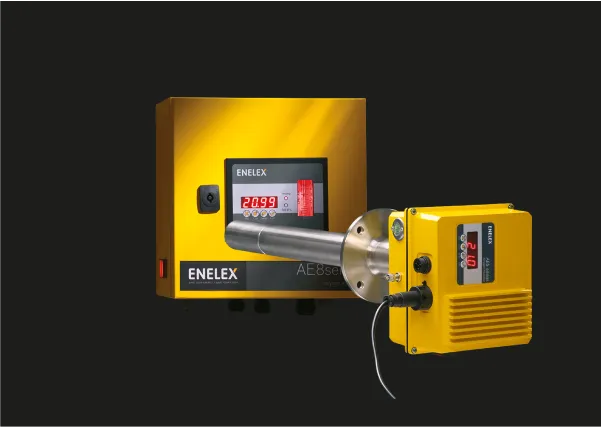
Analyzátory kyslíku
Analyzátory kyslíku
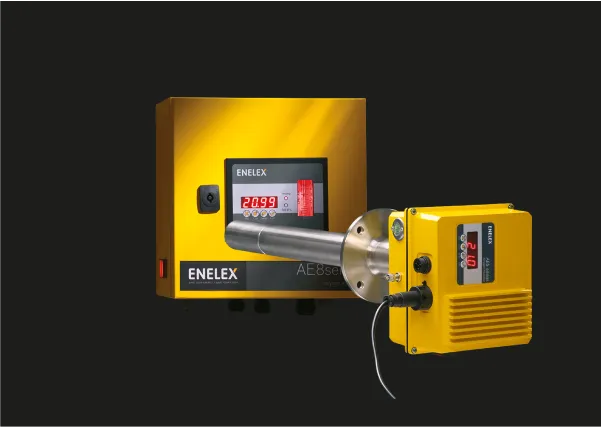
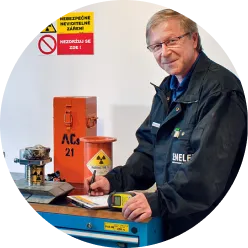
Radiační ochrana
Radiační ochrana
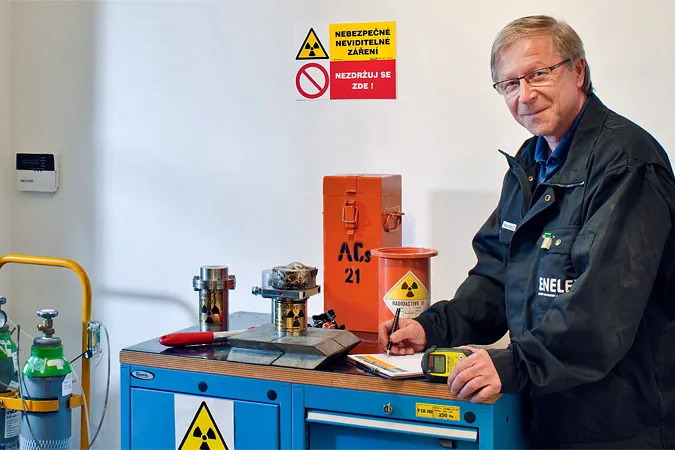
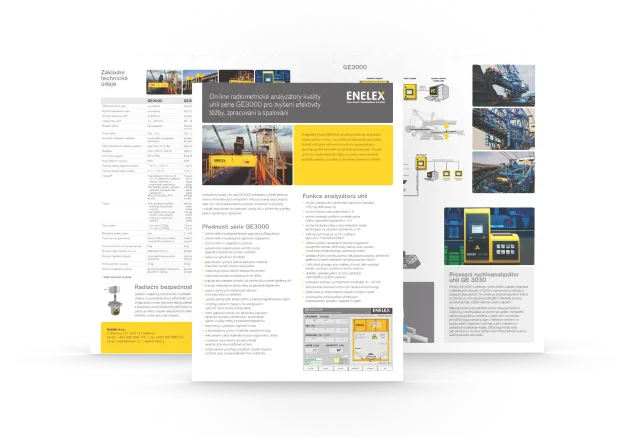